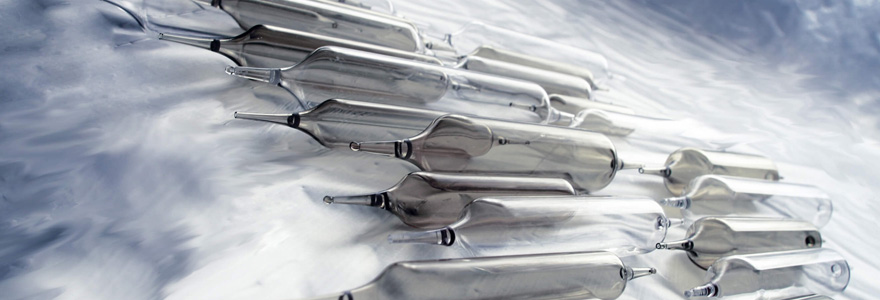
This article discusses the manufacture of double-ended glass ampoules for pharmaceutical/nutraceutical use. Double-ended ampoules are ampoules that have two openings, one at each end, and are used to hold a variety of liquids. The manufacturing process for these ampoules is described in detail, including the materials needed and the steps involved.
Making double-ended glass ampoules for pharmaceutical/nutraceutical use
The manufacture of double-ended glass ampoules for pharmaceutical/nutraceutical use is a process that involves the use of two pieces of glass tubing that are fused together at their ends. The process begins by heating the two pieces of glass tubing in a furnace until they are soft enough to be bent. Once the glass is soft enough, it is then placed in a mold that will give it the desired shape. After the glass has cooled and hardened, it is then cut to the desired length and the ends are sealed. The sealed ampoules are then placed in an annealing oven where they are slowly cooled to relieve any stresses that may have been placed on the glass during the manufacturing process. More on sfamgroup.com.
What type of glass is used in ampoules?
Ampoules are small, sealed glass containers that are used to hold various substances, including pharmaceuticals and nutraceuticals. The glass used in ampoules must meet certain criteria in order to be suitable for use; it must be durable, chemically resistant, and able to withstand the high temperatures involved in sterilization. Double-ended ampoules are those that have a neck on each end, as opposed to a single-ended ampoule, which has a neck on one end and a flat bottom on the other. The manufacturing process for double-ended ampoules is as follows:
First, the glass is cut to the desired size and shape. Next, the necks of the ampoule are formed. This is done by heating the end of the glass rod until it is soft enough to be shaped, and then forming it into the desired shape. After the necks are formed, the bottom of the ampoule is sealed. This is done by heating the bottom of the glass until it is soft and then pressing it onto a flat surface to seal it. Finally, the ampoule is trimmed and any sharp edges are smoothed.
The finished product is a double-ended ampoule that is ready to be filled with the desired substance. Ampoules are a convenient and safe way to store and transport pharmaceuticals and nutraceuticals, and the glass used in their manufacture must meet strict standards in order to ensure the safety of the contents.
What is the difference between Type 1 and Type 2 glass?
Ampoules are small, sealed glass containers that are used to hold injectable solutions, powders, and other small volumes of material. They are typically made of Type 1 or Type 2 glass, which refers to the way the glass is formed. Type 1 glass is made by blowing and shaping the glass into a mold, while Type 2 glass is made by drawing it out into a long, thin tube and then cutting it to the desired length.
Double-ended ampoules are those that have a neck at each end, which allows them to be used for both injection and withdrawal of the contents. These ampoules are typically made of Type 1 glass, as the blowing process makes it easier to create the double-ended structure.
The manufacturing process for double-ended ampoules begins with the creation of a parison, which is a long, tubular piece of glass. The parison is then placed into a mold that has the desired shape of the ampoule. The mold is then closed and heated, causing the glass to soften and take on the shape of the mold.
Once the ampoule has cooled and hardened, the neck of each end is cut to the desired length and the ampoule is then ready for use. Double-ended ampoules are typically used for pharmaceutical and nutraceutical applications, as they provide a sterile, air-tight container for these products.
The article discusses the manufacture of double-ended glass ampoules for pharmaceutical/nutraceutical use. The ampoules are made by a process called "drawing" in which a tube of glass is heated and then pulled to form a thin, hollow tube. The ends of the tube are then sealed and the ampoule is ready for use. The article describes the process in detail and provides information on the equipment and materials needed for the process.